انتخاب روغن هیدرولیک مناسب
مایع هیدرولیک یکی از مهمترین اجزای سیستم هیدرولیک است. عملکردهای متعددی مانند انتقال قدرت، روانکاری، انتقال حرارت، انتقال لجن و آلودگی های سایشی و ... را انجام می دهد. با توجه به نقش های مهم مایعات، انتخاب سیال مناسب برای به حداکثر رساندن عملکرد و عمر پمپ های هیدرولیک، موتورها و سایر قطعات بسیار مهم است. برای انتخاب صحیح، باید انواع خواص سیال را در کنار سایر عوامل مانند پارامترهای عملکرد، الزامات سیستم، شرایط محیطی و مقررات قابل اجرا در نظر گرفت.
تاثیر روغن های روانکار بر عملکرد پمپ
اجزای هیدرولیک و روانکار با یکدیگر کار می کنند تا سیستم هیدرولیک را اجرا کنند. از آنجا که سیال واسطه ای است که قدرت را برای انجام هر کار قابل استفاده منتقل می کند ، سیستم های هیدرولیک به سادگی نمی توانند بدون سیال یا روغن کافی کار کنند.
با توجه به نقش حساس روغن هیدرولیک ، نوع روغن مناسب ، ویسکوزیته و کیفیت از ملزومات اساسی برای انتخاب سیال می باشد. یک سیستم هیدرولیک با سیال نامناسب ممکن است کار کند اما عملکرد غیر استاندارد را ارائه می دهد ، که در نهایت می تواند منجر به خرابی های فاجعه بار شود. انتخاب نامناسب سیالات می تواند نتایج نامطلوب مختلفی را ایجاد کند ، مانند کاهش کارایی سیستم ، عدم روانکاری ، کاهش عمر سیال و اجزاء ، خوردگی ، فرسایش ، تشکیل لجن و لاک و تولید گرمای بیش از حد.
علاوه بر خواص و کیفیت سیال ، آلودگی بر عملکرد سیستم نیز تأثیر قابل توجهی می گذارد. آلودگی به طور کلی می تواند از چند منبع ناشی شود: روغن آلوده ، آلودگی داخلی ، آلودگی وارد شده و ... این امر می تواند منجر به کاهش کارایی، فرسودگی قطعات و سایر آثار منفی شود. مطالعات نشان می دهد که بیش از 70 درصد خرابی های سیستم هیدرولیک به دلیل آلودگی است و قبل از تشخیص نقص سیستم، بازده هیدرولیکی می تواند تا 20 درصد کاهش یابد.
خواص سیال را باید در نظر گرفت
خواص مختلف سیال بر توانایی سیال در انجام عملکردهای مختلف تأثیر می گذارد. گرانروی، که مقاومت سیال در برابر جریان را توصیف می کند یکی از مهمترین آنها می باشد. روغنکاری هیدرودینامیکی/مرزی، بازده حجمی، کارایی مکانیکی، کاویتاسیون، مقدار روان کننده هایی که به قطعات روانکاری رسیده، تولید گرما و بسیاری دیگر از خواص مانند انتشار هوا ، اتلاف گرما و قابلیت فیلتراسیون را در بر می گیرد.
مایعات با ویسکوزیته پایین ضخامت لایه نازک را ایجاد می کنند ، که منجر به شرایط روانکاری مرزی می شود، که می تواند منجر به تماس فلز با فلز و آسیب به اجزای سیستم شود. به عنوان مثال ، هنگامی که دو سطح فلزی متحرک با روانکاری نامناسب با یکدیگر تماس می گیرند، ممکن است در اثر جوشکاری سرد و خرابی قطعات، سایش بیش از حد ایجاد شود، همانطور که در شکل یک نشان داده شده است.
از طرف دیگر، ویسکوزیته بالا یا مقاومت زیاد در برابر جریان، می تواند منجر به کندی عملکرد و کاهش راندمان مکانیکی شود. اتلاف انرژی ناشی از گرانروی زیاد می تواند منجر به افزایش دمای سیال شود. ویسکوزیته بالا می تواند باعث کاویتاسیون و خواص ضعیف رهاسازی هوا شود و در نتیجه منجر به فرسایش حفره ای و هوادهی شود، همانطور که در شکل دو نشان داده شده است. علاوه بر این ، روان کننده ها ممکن است به مناطقی با فاصله زیاد نرسند و به دلیل روانکاری نامناسب باعث خرابی شوند.
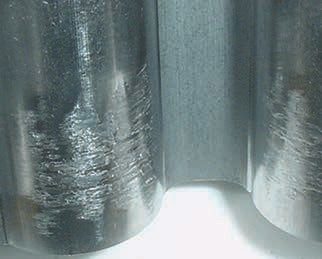
شکل 1. ویسکوزیته پایین می تواند باعث تماس فلز با فلز شده و منجر به خرابی قطعات شود.
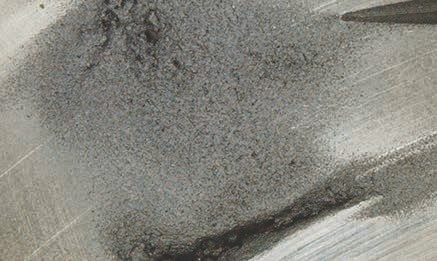
شکل 2. گرانروی زیاد می تواند منجر به کاویتاسیون و فرسایش ناشی از فروپاشی هوا یا حباب های خلاء شود.
میزان انتشار هوا بر اساس گرانروی و دماهای مختلف متفاوت است. در دمای معین، هوا با سیالاتی که ویسکوزیته پایین تری دارند سریعتر آزاد می شود ، همانطور که در شکل 3 نشان داده شده است ، با افزایش دما ، هوا نیز برای هر سیال سریعتر آزاد می شود.
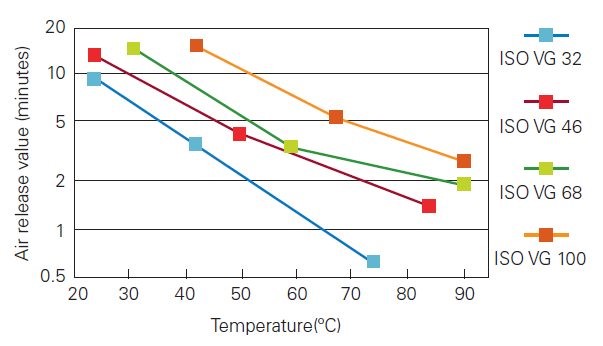
شکل 3. انتشار هوا بر اساس دما و ویسکوزیته متفاوت است.
گرانروی به خودی خود تحت تأثیر دما قرار می گیرد و عوامل موثری مانند دمای محیط ، دمای کارکرد و طراحی سیستم را تحت تأثیر قرار می دهد. سیال با درجه گرانروی مناسب باید برای هر کاربرد بر اساس دمای کار انتخاب شود. ویسکوزیته سیال در دمای کار باید توصیه های مربوط به ویسکوزیته اجزای سیستم، در درجه اول پمپ را برآورده کند. برای انتخاب درجه ویسکوزیته سیال باید حداقل ، حد معمول و حداکثر عملکرد در نظر گرفته شود.
راندمان کلی اجزای هیدرولیک به بازده مکانیکی و بازده حجمی مربوط می شود. کارایی مکانیکی سیستم مربوط به تلفات اصطکاکی و کشش ناشی از ویسکوزیته روغن است و کارایی حجمی مربوط به نشتی های داخلی است. هر دو بازده حجمی و مکانیکی به ویسکوزیته سیال بستگی دارد. همانطور که در شکل 4 نشان داده شده است ، بازده حجمی با افزایش ویسکوزیته افزایش می یابد در حالی که بازده مکانیکی با کاهش ویسکوزیته افزایش می یابد. محدوده خاصی از ویسکوزیته که در آن راندمان کلی حداکثر است معمولاً به عنوان بهترین انتخاب می شود.
شکل 4. محدوده عملکرد مطلوب یک سیستم هیدرولیک بستگی زیادی به ویسکوزیته سیال دارد.
خواص ضدسایش (AW) مایعات یکی دیگر از پارامترهای مهم است که باید مورد توجه قرار گیرد. خواص خوب ضدسایش برای به حداکثر رساندن عملکرد سیستم هیدرولیک و عمر قطعات مورد نیاز است. روغن روانکار باید به درستی فرموله شده و دارای افزودنی های کافی ضدسایش باشد. مواد افزودنی ضدسایش یک لایه نازک روی سطوح جفت گیری ایجاد کرده و از تماس فلز با فلز در شرایط روانکاری مرزی جلوگیری می کند. خسارت ناشی از عدم وجود خواص افزودنی های ضدسایش در شکل 5 نشان داده شده است.
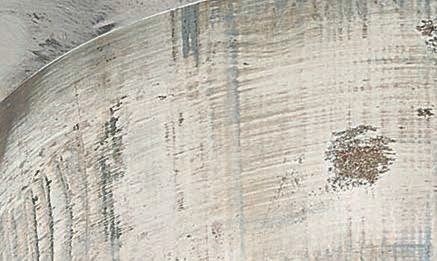
شکل 5. یک حلقه بادامک از پمپ پره ای به دلیل نداشتن خاصیت ضد سایش آسیب دیده است.
خواص ضدسایش ناکافی می تواند منجر به جوشکاری سرد و خراشیدگی در فرآیند روغن کاری مرزی شود که منجر به حذف مواد سطحی می شود. خواص ضد سایش هم برای تماس سایش های نوردی و هم برای سایش های کشویی ضروری است ، اما نیاز آن برای سایش های کشویی بسیار مهم است ، زیرا حرکت با نوع چسبندگی و لغزشی ممکن است رخ دهد. حتی بهترین سطوح ماشین کاری دارای ناهمواری (پستی و بلندی) هستند. هنگامی که ناهمواری ها با بار سنگین در تماس هستند ، می توانند با جوشکاری سرد به هم متصل شوند. اگر نیروی وارد شده به اندازه کافی بزرگ باشد که جوش را بشکند، جسم ناگهان حرکت می کند و این باعث حذف مواد از سطوح می شود به همین منظور برای کاربردهای شدید با نیروی بالا افزودنی ضدسایش زیاد توصیه می شود، به طوری که سطوح بدون هیچ گونه آسیب سطحی روی یکدیگر لغزیده یا روی هم بچرخند، همانطور که در شکل 6 نشان داده شده است.
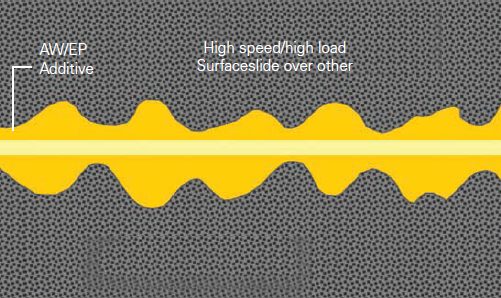
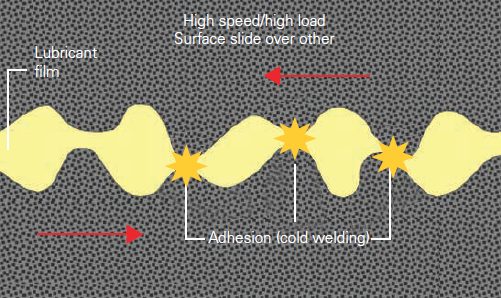
شکل 6: مواد افزودنی ضد سایش می توانند به لغزش سطوح بر روی یکدیگر و جلوگیری از حرکت "چسبندگی و لغزش" کمک کنند.
آزمایش پمپ برای نشان دادن توانایی سیال در محافظت از اجزا در برابر سایش ایجاد شد و در نتیجه می توان استفاده طولانی مدت در شرایط مختلف عملیاتی را تأیید کرد، این آزمایش توسط انجمن آزمایش و مواد آمریکا (ASTM) با تعیین6973 ASTMD (روش آزمون استاندارد برای نشان دادن ویژگی های سایش مایعات هیدرولیک نفتی در پمپ پرقدرت ثابت فشار بالا).
از آزمایش پمپ می توان برای ارزیابی خواص ضد سایش مایعات هیدرولیک استفاده کرد. مایعات با عملکرد بالاتر می توانند به طور چشمگیری سایش را کاهش داده و عمر قطعات را افزایش دهند ، همانطور که در شکل 7 نشان داده شده است.
شکل 7. نتایج آزمون پمپ که سیالات مختلف را آزمایش می کند.
سایر خواصی که باید در نظر گرفته شود عبارتند از:
- شاخص ویسکوزیته ( Viscosity Index (VI)): یک عدد تجربی ، بدون واحد و نشان دهنده تأثیر تغییر دما بر ویسکوزیته سینماتیکی یک روغن است. وقتی مایعات گرم می شوند ، ویسکوزیته آنها کمتر می شود. VI بالا نشان دهنده تغییر نسبتاً کمی ویسکوزیته با دما است. مایعات VI بالا (چند درجه ای) برای کاربردها در دمای عملیاتی وسیع یا در شرایط شدید محیطی توصیه می شود. به طور کلی ، مایعات VI بالا برای تجهیزات سیار توصیه می شود، زیرا در معرض تغییرات محیطی و درجه حرارت بالا هستند.
- پایداری برشی (Shear stability): میزان مقاومت سیال در برابر برش است. پلیمرها، که به عنوان بهبود دهنده های VI شناخته می شوند ، برای تولید مایعات VI بالا با پایداری برشی کم استفاده می شوند که به سرعت تجزیه می شوند و در نتیجه باعث نازک شدن روغن می شوند. ویسکوزیته سیال پس از برش نیز باید برای کاربردهایی که مایعات VI بهبود یافته دارند در نظر گرفته شود.
- پایداری حرارتی و اکسیداسیون (Thermal and oxidative stability): اکسیداسیون واکنش شیمیایی اکسیژن با روغن است که محصولات جانبی اسیدی تولید می کند. سرعت اکسیداسیون توسط دمای بالا ، آب و اسیدهای تولید شده در اثر اکسیداسیون و وجود کاتالیزورهای فلزی مانند مس افزایش می یابد. قانون کلی این است: اکسیداسیون با افزایش دما هر 10 درجه سانتیگراد دو برابر می شود. اکسیداسیون منجر به افزایش ویسکوزیته ، مقدار اسید کل (TAN) بیشتر ، وارنیش و لجن و تیره شدن مایع می شود. میزان اکسیداسیون را می توان با کاهش دمای سیال و استفاده از مایعات فرموله شده با ذخایر پایه با کیفیت ، افزودنی های آنتی اکسیدان و افزودنی های AW پایدار از نظر حرارتی محدود کرد.
- پایداری هیدرولیتیک (Hydrolytic stability): هیدرولیز تجزیه شیمیایی روان کننده ها در واکنش با آب است. مواد افزودنی روان کننده ، به ویژه افزودنی های حاوی روی ، با آب واکنش داده و محصولات جانبی اسیدی را تشکیل می دهند. وجود فلزاتی مانند مس می تواند نقش کاتالیزور را ایفا کند. ذخایر پایه از نوع استر نیز در حضور آب هیدرولیز می شود. روان کننده ها با پایداری هیدرولیتیک خوب در برابر هیدرولیز مقاومت می کنند.
- قابلیت فیلتراسیون (Filterability): فیلترهای ریز مورد استفاده در سیستم های هیدرولیک ممکن است به دلیل فرمولاسیون نامناسب ، آلودگی آب و تخریب مایع ، فیلتر را زود هنگام ببندند. اندازه گیری قابلیت تصفیه به پیش بینی رفتار سیال در کاربردهای فیلتراسیون قبل از استفاده در سیستم کمک می کند.
- شفافیت پذیری (Demulsibility): توانایی آزادسازی آب از مخلوط آب و روغن. این ویژگی برای تجهیزات مورد استفاده در آب و هوای مرطوب که احتمال آلودگی آب زیاد است ، مهم است.
- مهار زنگ زدگی و خوردگی (Rust and corrosion inhibition): مایعات هیدرولیک به طور کلی با مهار کننده های زنگ زدگی و خوردگی فرموله می شوند. بازدارنده های زنگ زدگی به صورت یک لایه نازک روی سطوح فلزی قرار می گیرند و محافظت در برابر زنگ زدگی را ممکن می سازند. مواد افزودنی ضد خوردگی مانع از هیدرولیز شده و از تشکیل مواد اسیدی جلوگیری می. قابلیت مایع برای جلوگیری از زنگ زدگی و خوردگی را می توان با آزمایش زنگ زدگی با استفاده از آب مقطر ، آب نمک و یک نمونه فولادی اندازه گیری کرد.
- سازگاری مواد (Material compatibility): در سیستم های هیدرولیک مواد لاستیکی و الاستومر ، از جمله شیلنگ ، مخزن های انباشت ، مهر و موم و واشرها ، در استفاده می شوند. به دلیل ترکیبات مختلف این اجزا ، مایعات برای سازگاری با الاستومرهای متداول مورد آزمایش قرار می گیرند تا عمر و عملکرد آنها را با آن مایع خاص پیش بینی کنند.
- آزاد سازی هوا (Air release): هوای ورودی معلق می تواند باعث ایجاد ناهنجاری های زیادی از جمله کارایی ضعیف سیستم ، خرابی سیستم از طریق فرسایش (مشابه کاویتاسیون) و تخریب سیال از طریق میکرو دیزل شود. میکرو دیزل زمانی اتفاق می افتد که حباب های هوا از یک منطقه با فشار کم یا منفی به یک منطقه با فشار بالا منتقل می شوند و در اثر فشرده سازی گرم می شده و در نتیجه محصولات جانبی کربن و اکسیداسیون ایجاد می شود. ویژگیهای رهاسازی هوا در سیستم هایی با زمان باقی مانده نسبتاً کوتاه اهمیت بیشتری دارد. یک آزمایش رهاسازی هوا می تواند توانایی یک روان کننده را در جدا کردن هوای ورودی مشخص کند.
- تمایل به کف کردن (Foaming tendency): کف کردن یک مشکل رایج در سیستم های هیدرولیک است. حجم زیاد فوم می تواند باعث سرریز شدن مخازن شود. عواملی که منجر به کف شدن می شوند عبارتند از: آلودگی ، تجزیه مایع ، جذب هوا و طراحی ضعیف سیستم. فرمولاسیون مایع هیدرولیک حاوی مهار کننده های ایجاد کف است ، اما دزهای بسیار زیاد می تواند عوارض جانبی ایجاد کند. آزمایش ایجاد و پایداری کف ، حجم کف تولید شده بلافاصله پس از همزن و هوادهی مایع را توصیف می کند. این آزمون حجم باقی مانده کف پس از زمان مشخصی از توقف هوادهی را اندازه گیری می کند.
همچنین برای کاربردهای خاص مانند برنامه های سازگار با محیط زیست و مقاوم در برابر آتش ، گاهی از مایعات متناوب مانند استرهای فسفات ، پلی استرها ، پلی اترهای پلی اتر ، پلی آلکیلن گلیکول ها ، مایعات بر پایه روغن گیاهی ، گلیکول آب و امولسیون های معکوس استفاده می شود. به عنوان مثال ، اگر مقاومت در برابر آتش بسیار مهم است ، خواص مقاوم در برابر آتش ممکن است مهمترین عامل باشد. به طور مشابه ، در کاربردهای حساس به محیط زیست ، تمرکز بر تجزیه پذیری و سمیت می باشد. انواع دیگر مایعات ، مانند مایعات غذایی و مایعات مشخصات نظامی ، گاهی در کاربردهای هیدرولیکی استفاده می شوند.
eaton
ترجمه: مسعود عابدین – واحدمارکتینگ