روغن پایه (Lubricant Base Oils)
روغن پایه (Lubricant Base Oils)
روانساز های مایع:
مهمترین روانساز های مایع، روغن های روانکننده (Lubricating Oils) هستند که به منظور کاهش اصطکاک و جلوگیری از فرسودگی قطعات فلزی متحرکی که با یکدیگر در تماس هستند به کار میروند. این هدف با ایجاد لایه نازکی از روانکننده بین قطعات عملی میشود.
هر روغن روانکننده از یک روغن پایه (Base Oil) و انواع مواد افزودنی (additives) برای دربر داشتن مشخصات مورد نیاز، تشکیل شده است.
روغن های پایه عمده ترین جزء تشکیل دهنده روغن های روانکننده هستند و به طور کلی به سه دسته معدنی (Mineral) ، سنتزی (Synthetic) و طبیعی (Natural) تقسیم می شوند.
1- روغن پایه معدنی (Mineral):
روغن پایههای معدنی شامل دو گروه روغنهای پارافینیک و نفتنیک که از تصفیه نفت خام به دست میآیند میباشند.
روغن های پارافینیک:
امروزه بیشتر روانکارهای مورد استفاده در ماشینآلات از روغنهای پارافینیک ساخته میشوند. این روغنها را هیدروکربنهای نرمال و هیدروکربنهای ایزو (شاخهدار) تشکیل میدهند. مولکولهای پارافینیک میتواند در دمای پایین، تشکیل کریستالهای واکس بدهند. روغن پارافینیک مخلوطی از هیدروکربنهای مختلف است و قسمت عمده واکس موجود در آن توسط فرآیند واکس زدایی از روغن خارج میشود. در مقایسه با روغنهای نفتنیک، روغنهای پارافنیک دارای خواص زیر هستند:
- مقاومت بالا در مقابل اکسیژن
- دمای ریزش بالاتر
- شاخص گرانروی بالاتر
- فراریت کم و در نتیجه نقطه اشتعال بالا
- وزن مخصوص کم
روغنهای نفتنیک:
روغنهای نفتنیک هیدروکربنهای حلقوی سیرشده یک یا چند حلقهای میباشند. این روغنها در مقایسه با روغنهای پارافنیک دارای خواص زیر هستند:
- مقاومت نه چندان خوب در مقابل اکسید شدن
- نقطه ریزش پایینتر به دلیل نداشتن واکس
- شاخص گرانروی پایینتر
- فراریت بالاتر و در نتیجه نقطه اشتعال پایینتر
- چگالی نسبی بالاتر
- خاصیت حل کنندگی بهتر
به طور کلی برای محدوده دمایی کم و هنگامی که نقطه ریزش پایین مورد نیاز باشد به کار گرفته میشوند.
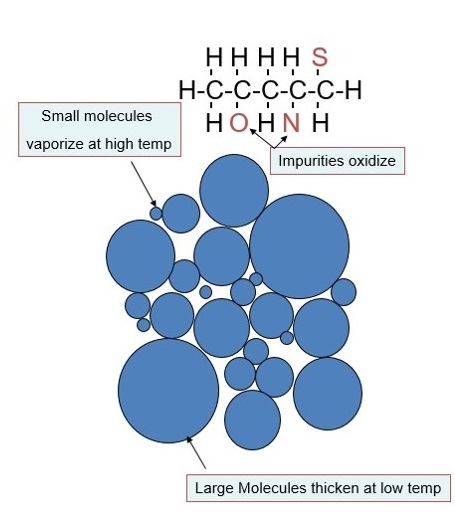
روغن های پایه معدنی از پالایش نفت خام به دست می آیند:
نمودار کلی فرآیند نفت خام و تولید روغن پایه در کشورمان در زیر نمایش داده شده است.
شرح فرآیند:
نفت خام با ورود به پالایشگاه، از مبدل های حرارتی (Heat Exchangers) عبور کرده وارد کوره می شود و پس از گرم شدن به برج تقطیر در اتمسفر (Atmospheric Tower) که دارای سینی های غربالی (sieve tray) می باشد انتقال می یابد و با انجام عملیات تقطیر جز به جز و به ترتیب محدوده نقطه جوش، هیدروکربن های متشکلهی آن، به گاز های سبک (C1 تا C5)، نفتای سبک و سنگین (و نهایتا بنزین موتور)، بلندینگ نفتا (نهایتا انواع حلال)، نفت سفید (Kerosene)، نفتگاز (Gas Oil)، و نفت کوره (Fuel Oil) تبدیل می شوند.
باقیمانده برج اتمسفریک به برج تقطیر در خلاء (Vacuum Tower) با سینی های کلاهکی (Bubble Cup) منتقل می شود و تحت خلاء (فشار 28mmHg) و حرارت، تفکیک می شود. از بالای برج، نفتگاز موم دار (آیزوفید) به واحد آیزوماکس منتقل می شود تا از آن نفتگاز و نفتسفید با کیفیت بالا (سوخت هواپیمای مسافربری) تولید شود و از بخش پایین تر (اواسط برج)، برشی به عنوان لوبکات (روغن خام) خارج می گردد که به واحد روغنسازی (Lube Oil Plant) منتقل می شود و طبق نمودار بالا و به روش استخراج با حلال (Solvent Extraction) به انواع روغن پایه (با توجه به گرانروی لوبکات) تبدیل می گردد.
در واحد روغنسازی، طی سه مرحله عملیات (برای روغن های پایه کیفیت بالا) و دو مرحله عملیات (برای روغن های پایه معمولی)، لوبکات پالایش و به روغن پایه تبدیل می شود. شرح اهداف و عملیات به صورت زیر است:
جدا کردن ترکیبات نامطلوب آروماتیک و بالا بردن مقاومت روغن در مقابل اکسید شدن:
وجود ترکیبات آروماتیک (حلقوی غیر اشباع) در روغن سبب می شود تا در مقابل حرارت به سرعت اکسید شود، لذا در مرحله اول و با انجام عملیات استخراج با حلال فورفورال، ترکیبات آروماتیک از روغن جدا شده و به عنوان فورفورال اکسترکت از واحد خارج می گردد. این محصول فرعی (جانبی)، در بازار تحت عنوان RPO (Rubber Process Oil)، روغن فرآیند لاستیک سازی، بفروش می رسد. بازار هدف آن عمدتا کشور هندوستان است.
محصول اصلی این واحد که به "واحد فورفورال" معروف است، رافینیت (Rafinate) است که در واقع لوبکات آروماتیک زدایی شده می باشد و شاخص گرانروی آن بالاتر رفته است.
به طور کلی در فرآیند استخراج "Extraction"، خوراک ورودی به واحد، با حلال مناسب "Selective Solvent" به نسبت مشخص و طراحی شده و زمان لازم تماس داده می شود.
حلال ترکیبات نامطلوب را در خود حل کرده و به عنوان "Extract" از بخش پایین سیستم خارج می شود، محصول که رافینیت "Rafinate" نامیده می شود از سمت دیگر سیستم به واحد بعدی منتقل می گردد.
انتخاب نوع حلال مناسب به عوامل زیر وابسته است:
• حداکثر قدرت حل کردن ترکیبات نامطلوب در خود را داشته باشد و منجر به تولید رافینیت با کیفیت بالا شود.
• حداقل خاصیت حل کنندگی روغن را داشته باشد و راندمان عملیات را کاهش ندهد.
• به سادگی بتوان اکسترکت را از رافینیت جدا نمود.
• مشخصاتی نظیر پایداری، سمیت کم، قیمت مناسب، سهولت تامین و حمل آسان برای حلال مورد توجه است.
• چنانچه بازیافت حلال مورد نظر باشد، حلالی مناسب خواهد بود که نقطه جوش آن از نقطه جوش اکسترکت و رافینیت کمتر باشد.
• حلال مناسب برای استخراج مواد آروماتیک از لوبکات، فورفورال است که یک آلدئید حلقوی به فرمول مولکولی C5H4O2 می باشد. گرانروی پایینی دارد و حلالیت آن برای روغن بسیار کم است. از معایب آن، اکسید شدن در مجاورت هوا و تولید ترکیبات اسیدی خورنده است. در دمای بالاتر از 230 درجه سلسیوس نیز تجزیه می شود.
برای تماس بیشتر حلال با خوراک، در فرآیند استخراج، از تکنیک های زیر استفاده می شود:
• استفاده از استخراج کنندههای (Extractors) گریز از مرکز جهت سهولت و تسریع در جدا نمودن اکسترکت از رافینیت.
• استفاده از وسایل مخلوط کن چند مرحله ای.
• استفاده از کنتاکتورهای صفحه گردان در ستون استخراج (روش های دیگر).
پارامترهای مهم در انتخاب حلال مناسب:
- حلالیت خوب روغن و حلالیت کم واکس در آن (نسبت کم حلال مصرفی به روغن)
- پایداری، سمیت کم، امکان تامین، قیمت مناسب و سادگی حمل و نقل
- آسان بودن بازیافت حلال (در صورت تمایل به بازیافت)
حذف گوگرد، نیتروژن، اکسیژن و حذف آروماتیک ها از روغن پایه:
برای تولید روغن های پایه مرغوب و با کیفیت بالا (پایه 2 و 3)، بعد از مرحله موم گیری، رافینیت خروجی که همان روغن پایه معمولی (پایه1) است را به واحد هایدرو فینیشینگ (Hydro Finishing Unit) منتقل نموده و با استفاده از هیدروژن، عملیات اشباع نمودن پیوندهای دوگانه، باز کردن حلقه آروماتیک، حذف آروماتیک ها، حذف گوگرد، نیتروژن و اکسیژن در مجاورت کاتالیست انجام و روغن پایه مرغوب تولید می نمایند.
این روغن ها که دارای شاخص گرانروی (VI) بالا، پایداری بیشتر در مقابل اکسیداسیون، درصد هیدروکربن های اشباع بالا و رنگ شفاف تر و گوگرد پایین تر هستند، برای تولید روغن های روان کننده با سطح کیفیت (Performance Level) بالا بمنظور استفاده در دستگاه ها و ماشین آلات حساس صنعتی، صنایع هواپیمایی، دریایی و سایر صنایع پیشرفته مورد استفاده قرار می گیرند.
طبقه بندی کلی روغن های پایه معدنی (Mineral Base Oils)
روغن های پایه معدنی به دو گروه کلی زیر تقسیم بندی می شوند:
- روغن های پایه پارافینی "paraffin base oil" که از نفت خام از نوع پارافینی بدست می آیند. نفت خام های ایران از این نوع هستند.
- روغن های پایه نفتنی " naphthenic base oil" که از نفت خام از نوع نفتنی بدست می آیند. حوزه های نفتی کشورهای همسایه شمالی از این نوع هستند.
روغن های پایه پارافینیک در مقایسه با روغن های پایه نفتنیک دارای خواص زیر هستند:
• مقاومت بالاتر در برابر اکسیداسیون
• شاخص گرانروی بالاتر (تغییر کم تر در مقابل دما)
• نقطه اشتعال بالاتر (فراریت کم)
• نقطه ریزش بالاتر (تشکیل کریستالهای واکس با کاهش دما)
• چگالی نسبی کمتر
روغن های پایه نفتنیک برای استفاده در محدوده دمایی پایین و مناطق سردسیر و نیز سیستم های سرد کننده مناسب هستند زیرا نقطه ریزش پایین تر دارند و حتی در دما های بسیار پایین تشکیل واکس (عدم سیّالیت) در آنها دیده نمیشود، اگرچه در سایر شاخصه های ذکر شده در بالا نسبت به روغنهای پایه پارافینیک مرغوبیت کمتری دارند.
معرفی تکنولوژی جدید هایدروپروسسینگ (Hydro Processing) در فرآیند تولید روغن پایه:
در شرح فرآیند تصفیه لوبکات و تولید روغن پایه به روش حلال، آنچه در کشورمان انجام می شود، بیان شده است و محصولات خروجی برج تقطیر در خلاء عبارتند از : نفت گاز موم دار یا آیزوفید (Vacuum Gas Oil) ، روغن خام (Lube Cut) و ...
در روش حلال، از لوبکات به عنوان خوراک برای تولید روغن پایه استفاده می شود ، لکن در روش های هایدرو پروسسینگ ، نفتگاز موم دار یا آیزوفید بعنوان خوراک مورد استفاده قرار می گیرد و طی سه مرحله زیر، روغن پایه مرغوب پایه 2 (Group II) تولید می شود.
مرحله 1 – عملیات هایدرو کراکینگ
مرحله 2 – عملیات موم گیری کاتالیستی
مرحله 3 – عملیات هایدرو فینیشینگ
نمودار زیر فرآیند هایدرو پروسسینگ برای تولید روغن پایه از نفت گاز موم دار را نشان می دهد:
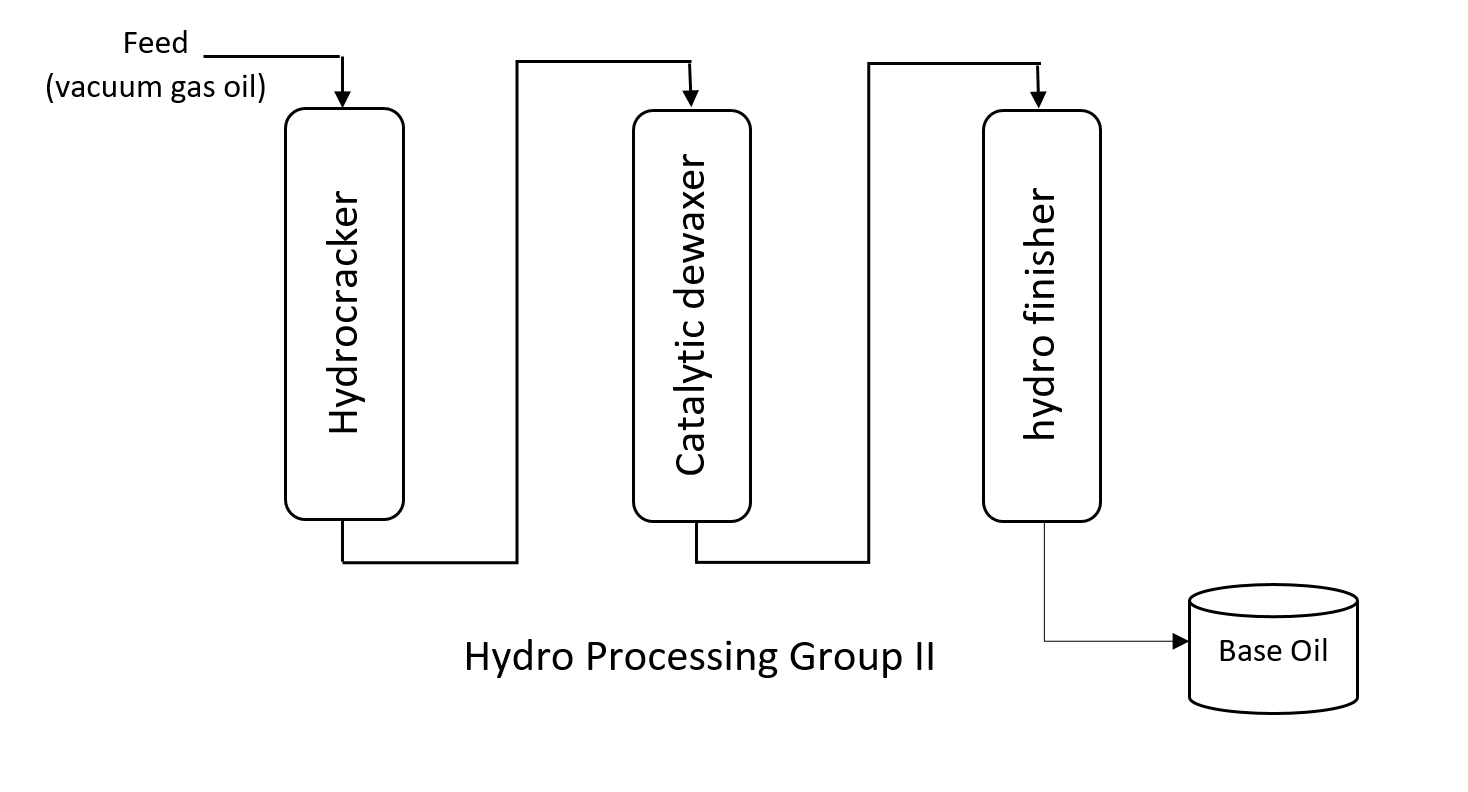
طبقه بندی API روغنهای پایه:
API موسسه نفت آمریکا (American petroleum institute) روغن های پایه نفتی (Mineral) را بر حسب کیفیت آن ها به سه گروه طبقه بندی نموده است:
• روغن های پایه گروه یک (تصفیه شده به روش حلال) : Group I
• روغن های پایه گروه دو (هیدروفرآوری شده/ هیدروژناسیون کاتالیستی): Group II
• روغن های پایه گروه سه (هیدروفرآوری شدید): Group III
جدول زیر طبقه بندی API روغن های پایه معدنی و مقایسه خواص آن ها را نشان می دهد:
معمولا روغن های پایه را با علامت SN که مخفف (Solvent Neutral) است به همراه یک عدد که تعیین کننده گرانروی آن است معرفی می کنند.
جدول زیر تنوع روغن های پایه تولید شده در کشور که بر حسب گرانروی کینماتیک (Kinematic Viscosity) در 100 درجه سلسیوس دسته بندی شدهاند را نشان می دهد:
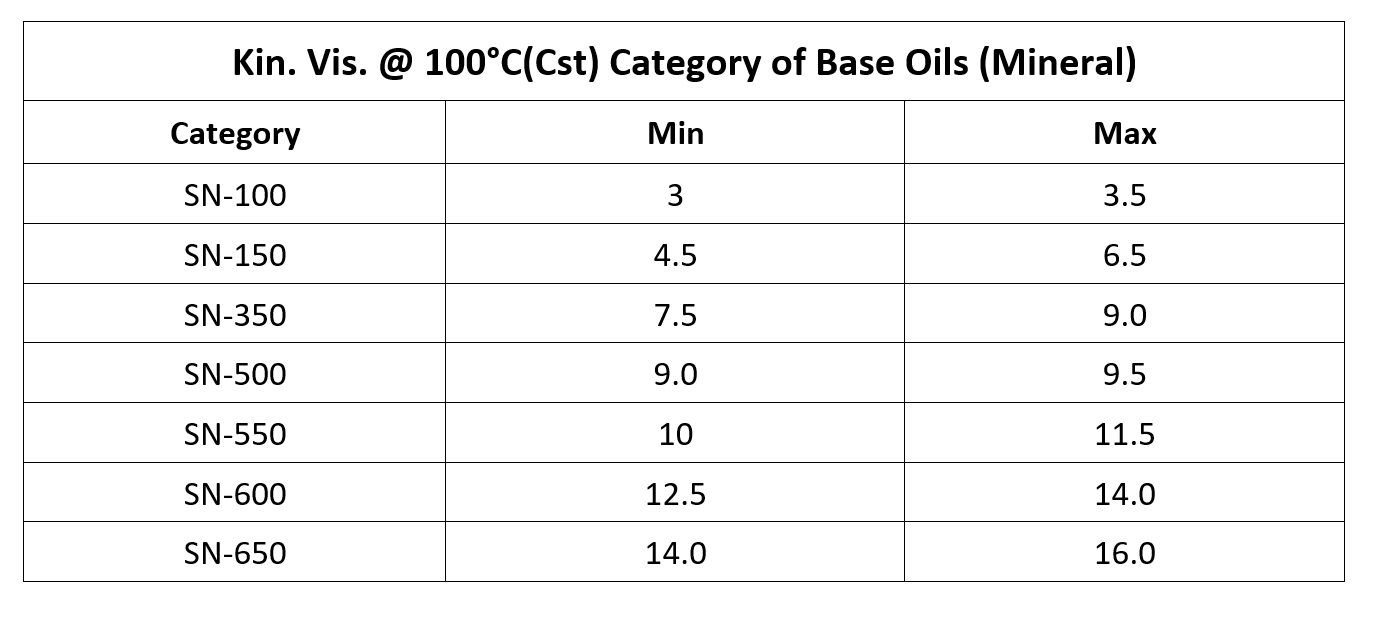
📋 استاندارد ملی ایران بشماره ISIRI 3299 (استاندارد روغن های پایه گروه یک در طبق بندی API)
دریافت استاندارد:
https://b2n.ir/479856
📋 استاندارد بین المللی ASTM D6074
(Standard Guide for Characterizing Hydrocarbon Lubricant Base Oils)
مشاهده استاندارد:
https://www.astm.org/Standards/D6074
2- روغن پایه سنتزی(Synthetic):
يك روغن پایه سنتزی محصولی است كه از يك واكنش شيميايی (سنتزی) دو يا چند تركيب ساده توليد شده كه حاوی افزودنی های ضروری می باشد. خوراك پايه كه شكل يك روانساز سنتزی دارد در يك فرايند بازسازی مولكولی قرار می گيرد تا خواص شيميایی و فيزيكی مورد نظر را به دست آورد.
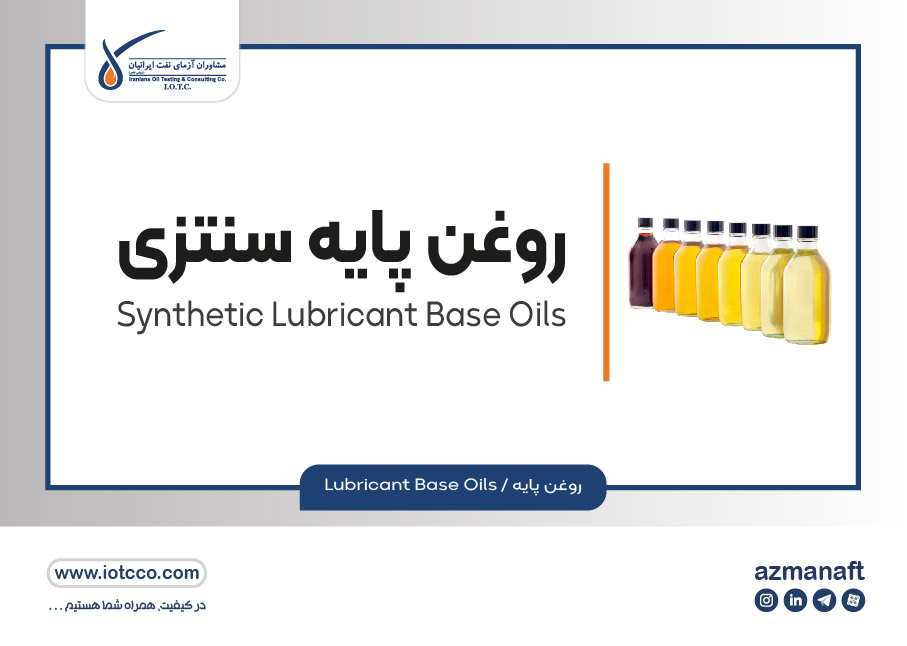
برخی از مهمترين و رايجترين روانسازهای سنتزی عبارتند از:
- سيالات پلی گلايكون - پلی آلكن گلايكول، پلی گلايكول اترها، پلی آلكالی گلايكول اترها
- سيليكونها
- استرها: (استرهای اسيدی دوعاملی)
- استرها: (استرهاي پلی نيوپنتيد)
- اولفين آلفا پيلمری شده: پلی آلفا اولفين، پليمرهای اولفينی، هيدروكربنهای سنتزی اولوگومری اولفينی
- آروماتيك آلكالی- دی آليكل بنزنها - يك هيدروكربن سنتزی
- استرها فسفاته

پلی آلفا اولفین ها:
اولفينهای آلفای پليمری يا پلی الفا اولفین ها یا PAO بطور معمول برای طراحی پليمرهای اولفينی و اوليه گومرهای الفينی استفاده می شوند. عبارت PAO اولين بار توسط شركت نفتی Gult استفاده شد اما امروزه به عنوان يك عبارت كلی برای هيدروكربنهای ساخته شده توسط اوليگومرازيسيون كاتاليستی اولفينهای آلفای خطی با شش يا بيشتر اتم كربن بكار می رود.
پلی گلیکول ها:
اين سيالات سنتزی در ابتدا درجاهایی استفاده می شد كه دما بسيار بالا بود. استفاده اولين از گلايكولها برای سيالات هيدروليك پايه آبی در نيروی دريایی ايالات متحده در سال 1943 بود. اين مواد روانكنندگی خوبی دارند، لجن بسيار كمي توليد می كنند، ايندكسر ويسكوزيته بالایی دارند و از پايداری حرارتی خوبی برخوردارند. كاربردهای آن شامل سيستم ترمز هيدروليك خودرو و (اتيلن و پلی اتيلن گلايكول)، روغنهای دنده صنعتی، سيالات مقاوم در برابر آتش (از مخلوط پلی گلايكول با آب)، گريسها، سيالات در تماس با فلزات و روغنهای فشردهكننده گاز می شود. پلی گلايكولها با روغن نفتی سازگار نيستند.
سیلیکون ها:
سيليكونها بدليل داشتن ايندكسر ويسكوزيته بسيار بالا، پايداری حرارتی خوب و عملكرد عالی در دمای پايين بطور گستردهای در سيستم ترمز خودرو و گريسها كاربرد دارند. سيالات ترمز سيليكونی پايداری حرارتی بسيار خوبی را دارند. سيال ترمز سيليكونی و سيال ترمز پلرگلايكولی به هيچ وجه قابل مقايسه با هم نبوده و چنانچه مخلوطی از اين دو استفاده شود قطعاً سيستم ترمز دچار آسيب جدی خواهد شد.
استرها:
در حين جنگ جهانی دوم روغنهای سنتزی توسعه يافتند. در اين ميان، استرهای با زنجيره طويل الكلی و اسيدها برای روانسازهای دمای پايين فوقالعاده بودند. پس از جنگ جهانی دوم، توسعه بيشتر استرها محدود به توربين گازی هواپيماها شد. در اوايل دهه 1960 استرهای نتيوپلراول برای اين هدف استفاده شد زيرا فراريت كم، نقطه اشتعال بالا و پايداری حرارتی خوبی داشتند.
تصفیه مجدد روغن های کارکرده:
تصفیه ی مجدد روغن های کارکرده و تبدیل به روغن های پایه اصلی در سال 1935 انجام شد. به روغن های بازیافتی پس از تصفیه ی مجدد روغن های تصفیه دوم گفته می شود. هزینه بالای فرایند و در نتیجه قیمت بالای فروش روغن های تصفیه ی دوم در مقایسه با قیمت تصفیه روغن های اول، حذف ناقص آروماتیک های چند حلقه ای سرطان زا، ظاهر نامناسب این روغن ها و افزایش پیچیدگی مخلوط های روغن پایه و روانکارهای دیگر در روغن موتور موجب استقبال کم از این روغن ها شده بود. در اروپای غربی در سال 1998 تنها 7 درصد از نیاز روغن پایه توسط محصولات حاصل از تصفیه ی دوم برطرف شده است. تصفیه ی مجدد روغن با توسعه ی استفاده از روغن در دنیا در سطح وسیعی مطرح بوده است. در کشور ما از 40 سال پیش آغاز شد. بر خلاف اکثر فرآورده های نفتی که تنها یک بار قابل استفاده هستند و از بین میروند چنانچه روغن مصرف شده به طور صحیح باز یابی گردد قابل استفاده مجدد می باشد.
بازیابی روغن های کارکرده را میتوان بخاطر عدم تغییر عمده در مواد تشکیل دهنده روغن پایه دانست.
فرآیند تصفیه دوم برای تمام روشهای موجود یکسان است. این مراحل عبارتند از:
1- جداسازی ناخالصی های جامد و آب موجود در روغن به وسیله فرآیندهای ته نشینی و آب گیری انجام می شود.
2- جداسازی اجزا فرار و باقی مانده سوخت (مانند بنزین و گازوییل )، حلال ها و اجزای روانکار با نقطه جوش کم، از روغن معمولا به کمک فرآیند تقطیر اتمسفریک انجام می شود. از هیدروکربن های سبک جدا شده می توان در تولید انرژی استفاده کرد.
3- جداسازی مواد افزودنی و محصولات جانبی حاصل از کهنگی (مانند لجن ها ،غیره …) به کمک فرآیند تصفیه با اسید، استخراج با حلال (پروپان) تقطیر در خلاء و تا حدی هیدروژنه کردن انجام می شود. حذف این مواد باعث افزایش دانسیته، شاخص گرانروی، طول عمر و بهبود رنگ روغن های کارکرده می شود.
4- جداسازی هر نوع ماده باقی مانده (مواد افزودنی، محصولات جانبی حاصل از کهنه شدگی و محصولات واکنش تصفیه) که توسط روش های انجام شده در مراحل قبل جدا نشده اند، توسط فرآیند پرداخت انجام می شود. فرآیند پرداخت معمولا توسط هیدرو پرداخت، جاذب هایی مانند خاک های رنگ بر و یا به کمک استخراج توسط حلال گزینه شی (مانند فورفورال) انجام می شود. هیدروپرداخت یک فرآیند با شرایط عملکرد متوسط، برای جدا کردن باقی مانده جزیی از مواد مضر (ترکیبات نیتروژن دار، اکسیژن دار، گوگرد دار و فلزات) از روغن است. این مرحله آخرین مرحله جدا سازی در تصفیه مجدد روغن های کارکرده است.
جهت بازیافت روغن کارکرده (سوخته) روش های مختلفی از جمله روش های تقطیر، استخراج با حلال، اسید و خاک، خاک و ... در دنیا وجود دارد که روش های ذیل عمده ترین روش های بازیافت روغن سوخته (کارکرده) می باشند.
1- تصفیه با اسید موسوم به روش اسیدی
2- تصفیه با خاک رنگبر (روش خاک)
3- روش تقطیر کامل
4- استخراج با حلال
روش اسیدی:
این روش یک متد 3 مرحله ای به شرح ذیل می باشد.
الف - تقطیراولیه؛ حرارت تاحدود (20±)360 درجه سانتیگراد
ب - اسید واش؛ سردنمودن روغن ومیکس آن باحدود 8٪ وزنی اسید سولفوریک وجداسازی لجن اسیدی پس از دو روز ماند
ج - تقطیر ثانویه و حرارت تا حدود320درجه سانتیگراد و میکس باخاک رنگبرحدود12٪ و پس از آن کاهش دمای روغن و ارسال به فیلتر پرس. این روش سه دسته تاسیسات لازم داشته ومصرف انرژی آن نیز بالا بوده و لجن اسیدی بزرگترین معظل آن بوده که هم اکنون به علت مخالفت شدید محیط زیست و مصرف انرژی بالا و 3 مرحله بودن و سرمایه گذاری اولیه درحال منسوخ شدن می باشد. در این روش فرایند تصفیه روغن سوخته حدود 4 روز زمان لازم دارد.
خاک بنتونیت خاصیت قطبی دارد و مواد اکسید شده در روغن هم قطبی هستند و وارد خاک می شوند و از روغن جدا می شوند و افزایش رنگ در روغن به خاطر این مواد اکسید شده در روغن می باشد.
در روش اسید با حذف پلیمر باعث افزایش پایداری برشی و با حذف فلز سبب کاهش خاکستر و همچنین با حذف ترکیبات آروماتیک شاخص گرانروی بالاتر و پایداری اکسیداسیون بیشتر می شود.
روش خاک:
این روش یک روش تک مرحله و فقط شامل قسمت ج روش اسیدی می باشد. در این روش روغن کارکرده به همراه یک ماده افزودنی و خاک رنگبرارزان قیمت همزمان وارد دیگ پخت می گردد. و فقط پس از یکبار حرارت دادن ، طی یک مرحله تولید به پایان رسیده ، سبکها جدا می گردند و ما بقی که شامل روغن و خاک رنگبر می باشد به فیلتر پرس فرستاده می شود، بعد از جداسازی خاک ، روغن پایه به دست می آید
در این تکنولوژی به سرمایه گذاری اولیه کمتری نسبت به روش اسید و تقطیر نیاز است. این تکنولوژی درحال جایگزینی روش اسیدی میباشد
تک مرحله ای بودن ومصرف انرژی ونیروی کار کم وسرمایه گذاری اولیه کمتر نسبت به روش اسیدی ازمزایای مهم آن است، که لجن اسیدی نیزنداردواز نظرکمی و کیفی قابل رقابت با روش اسیدی می باشد.دراین روش مصرف خاک رنگبر ارزان حدود (2±)23٪ می باشد
کل فرایند تصفیه در این روش کمتر از یک روز است.
تصفیه روغن کارکرده به روش تقطیری:
در کشور ایران آخرین روش شناخته شده در خصوص تصفیه روغن روش تین فیلم می باشد که بدلیل مقرون بصرفه بودن و پاک بودن نوع تصفیه مورد توجه قرار گرفته و اکثر تولیدکنندگان روش قدیمی در حال تغییر و روی آوردن به این تکنولوژی هستند. زیرا با این روش هیچگونه ضایعات باقی نمی ماند و همچنین از نظر زیست محیطی حد مطلوب رعایت می گردد.
پروسه تین فیلم به شرح ذیل می باشد:
در این روش روغن سوخته وارد ستون تقطیر گردیده و با ورش بویلرینگ و سیرکولاسیون حرارت می بیند، در این مقطع در دمای مختلف به روش های وکیوم بخارات متصاعد شده جمع آوری می گردد که با توجه به دما دسته بندی می گردد که شامل گازوئیل – روغن هیدرولیک پایه و روغن پنجاه پایه می باشد. در طول خط جهت جمع آوری گازها از مبدل ها و رسیورهای مختلف که با ظرفیت تولید هماهنگ می باشند استفاده گردیده که باعث انجام پروسه با کیفیت بالا صورت پذیرد. لازم به ذکر است که پس از تولید این روغن می بایستی سیستم تکمیلی جهت فراوری روغن تا رسیدن به روغن قابل مصرف صورت پذیرد.
مزایا روش تقطیر:
1- حذف کامل پلیمر
2- شکست مولکولی کم می شود وبازده روغن بالا می رود
3- چون فلزات تبخیر نمی شوند خاکستر کم می شود
4- باقی مانده را می توان به عنوان وکیوم باتوم در تولید قیر استفاده کرد
5- روش بسیار سریعی است
6- امکان گرفتن برش روغن داریم
تصفیه روغن سوخته به روش استخراج با پروپان
تکنولوژی IFP از مهمترین و اصلی ترین فرآیندهای استخراجی تصفیه است. روش IFP در ابتدا همواره با روش تصفیه با اسید و امروزه همواره با هیدروپرداخت انجام میشود. استفاده از پروپان همواره با تصفیه اسیدی در روش IFP شامل مراحل زیر میباشد:
1- گرم کردن روغن تا حدود 160 درجه سانتی گراد در فشار متعارفی برای خارج کردن آب، بنزین و مواد تشکیل دهنده با نقطه جوش پایین
2- استخراج با پروپان (PDA4) به منظور جدا سازی مواد آسفالتی و فلزات، این عمل در حرارت 30 الی 70 درجه و فشار 15 اتمسفر انجام می شود.
3- ترکیب با اسید سولفوریک غلیظ، در این روش اسید سولفوریک به مقدار کم مصرف می شود (در حدود 2درصد) و جداسازی ناخالصی ها
4- بی رنگ کردن به کمک خاک رنگبر در حرارت مناسب و فیلتراسیون آن به کمک فیلتر پرس و جداسازی گل آغشته به روغن
5- تبخیر در خلاء برای جدا سازی گازوییل، روغن دوک و انواع روغن های پایه
برتری این روش،کاهش مقدار اسید مصرف شده میباشد.
استفاده از پروپان و هیدروژن، این روش شامل مراحل زیر میباشد:
1- گرم کردن روغن تا حدود 160 درجه ساتی گراد در فشار متعارفی برای جداسازی آب، بنزین و مواد با نقطه جوش پایین
2- تصفیه مقدماتی با یک درصد آهک
3- استخراج با پروپان برای جداسازی مواد قیر و فلزات
4- هیدروژناسیون
5- مجاورت با خاک رنگبر (3در صد خاک ) در حرارت مناسب و تصفیه آن (جداکردن خاک) به کمک فیلتر پرس
6- تقطیر جز به جز در خلا به منظور جدا سازی برش های مختلف روغنی
[تمام مطالب مرتبط با روغن پایه (Lubricant Base Oils) در این صفحه بروزرسانی خواهد شد]